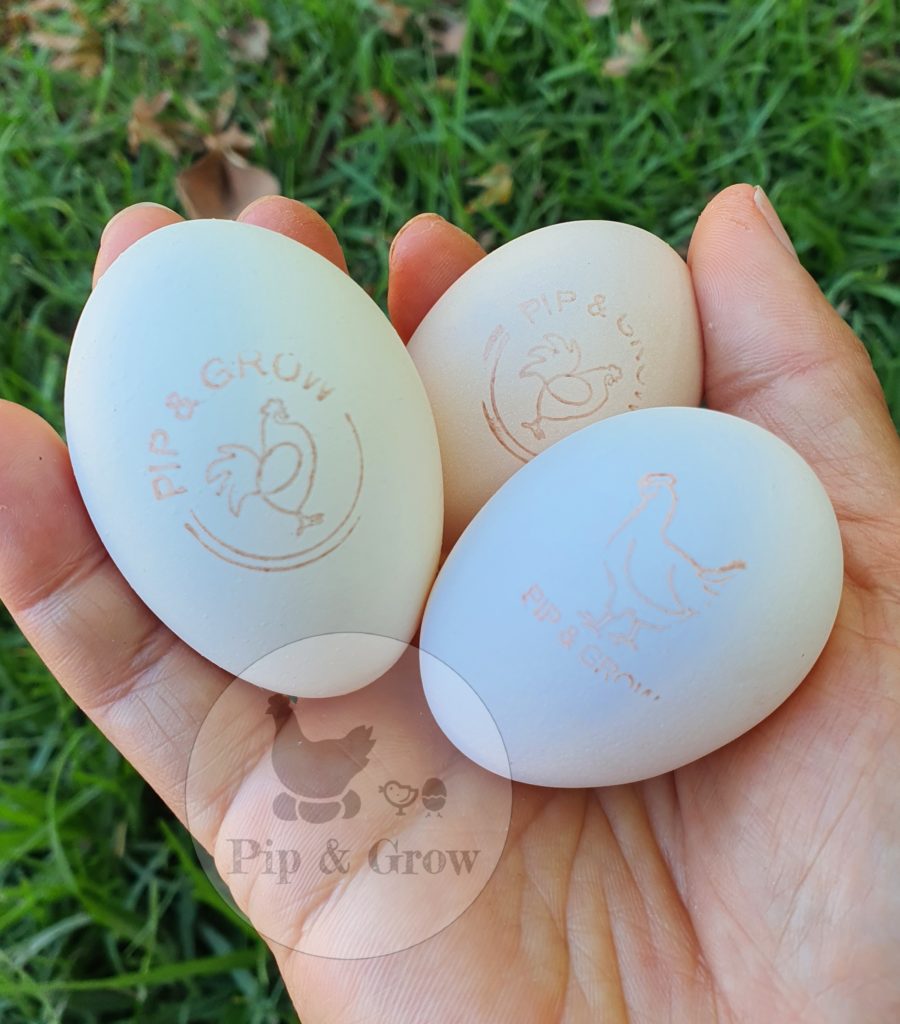
We’ve been providing fertile eggs across Australia, typically dispatching around 450-500 parcels per season from August to February annually. We’re proud to recognize returning customers each season, reflecting the satisfaction many have had with our eggs.
As a well-established small breeder in this industry, we understand the power of word-of-mouth and prioritize maintaining our reputation. While purchasing fertile eggs, especially through shipping, carries inherent risks, we rely on both statistics and community feedback to guide our practices. There’s simply no incentive for us to provide unsatisfactory or non-viable eggs to customers, knowing that any issues would quickly reach us.
Before listing fertile eggs for sale each season, we conduct rigorous testing to ensure that fertility levels surpass 85%. Moreover, we regularly hatch our own eggs on a weekly to fortnightly basis for local Day-old chick sales during the season, a process explicitly detailed on our website where orders are placed. If any eggs fail to meet our stringent standards or exhibit any issues with hatching, our policy is straightforward: we cease selling them.
While most of our eggs hatch at acceptable rates, we acknowledge that occasional instances may not yield the desired outcome. In these cases, we unfortunately bear the brunt of blame, often accused of selling unfertilized or poor quality eggs and facing demands for refunds or replacements. This post is written from the perspective of a breeder who offers fertile eggs to the public, aiming to explain the challenges we encounter in guaranteeing the quality of our eggs once they leave our care.
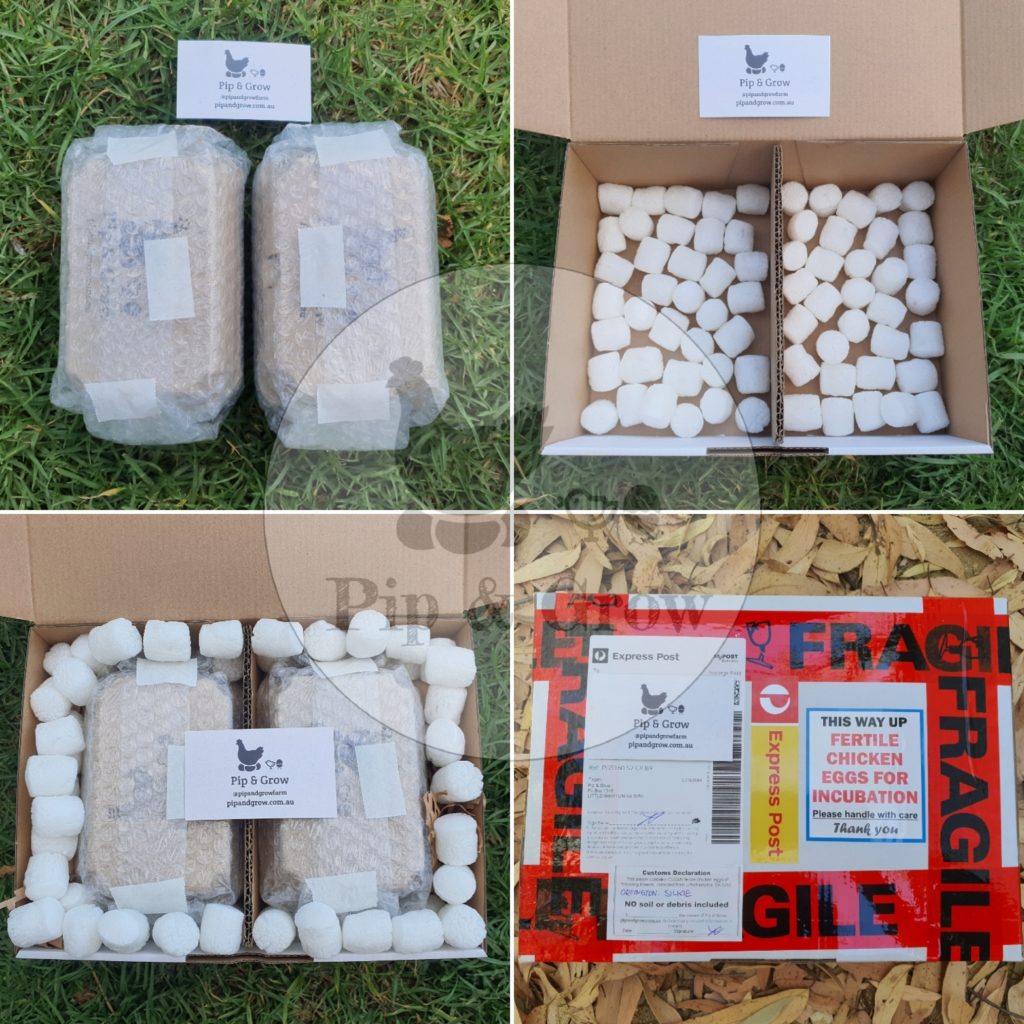
Once eggs leave our hands, we lose control over how they are handled. They may not have been transported safely after pickup, stored incorrectly, or left in hot or cold in the car. Posted eggs face numerous challenges, enduring being shaken in transit vehicles, potentially being stored upside down in bags, and jostled on sorting belts. There’s also the risk of them being dropped along the way, experiencing air pressure differences during flights, exposure to X-rays, and enduring fluctuating temperatures during transit and delivery.
Two batches of eggs, originating from different breeders, were incubated in the same incubator. While Lot A exhibited decent viability, Lot B showed no signs of development. This discrepancy does not necessarily indicate that the eggs in Lot B were inherently of poor quality. It is possible that Lot B experienced a challenging journey during shipping, resulting in internal damage severe enough to prevent embryo development.
These factors are entirely beyond our control. Despite our meticulous packaging efforts and the best intentions of our customers to handle the eggs carefully, accidents can occur. Unfortunately, there’s no way for us to monitor or mitigate these risks once the eggs are out of our possession.
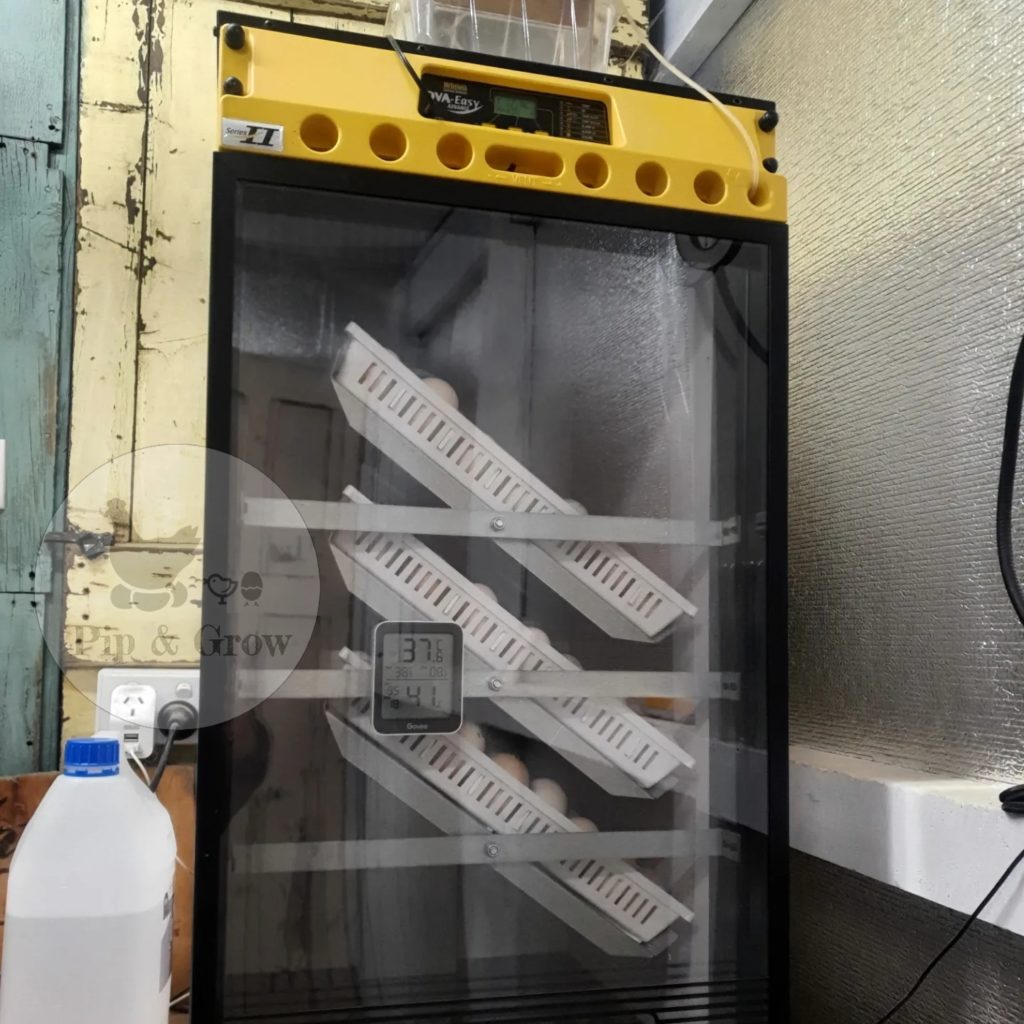
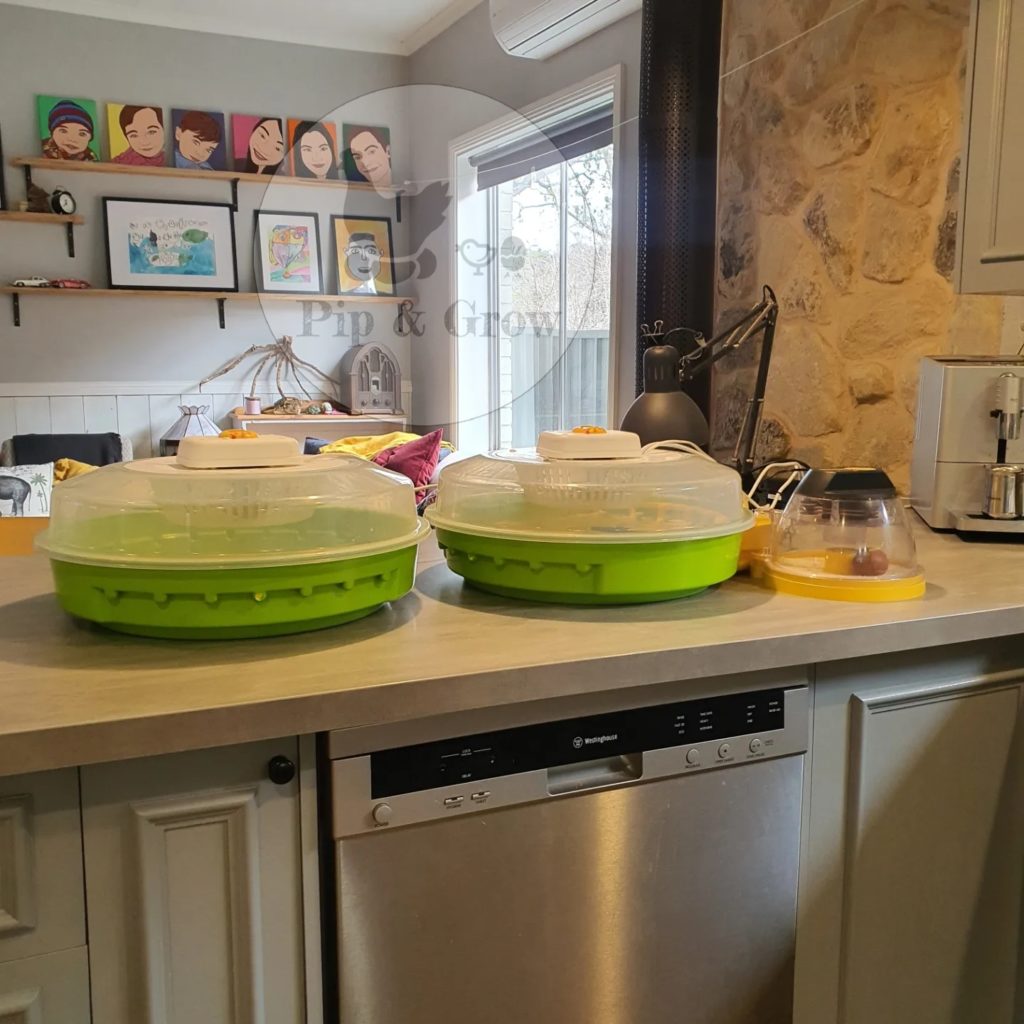
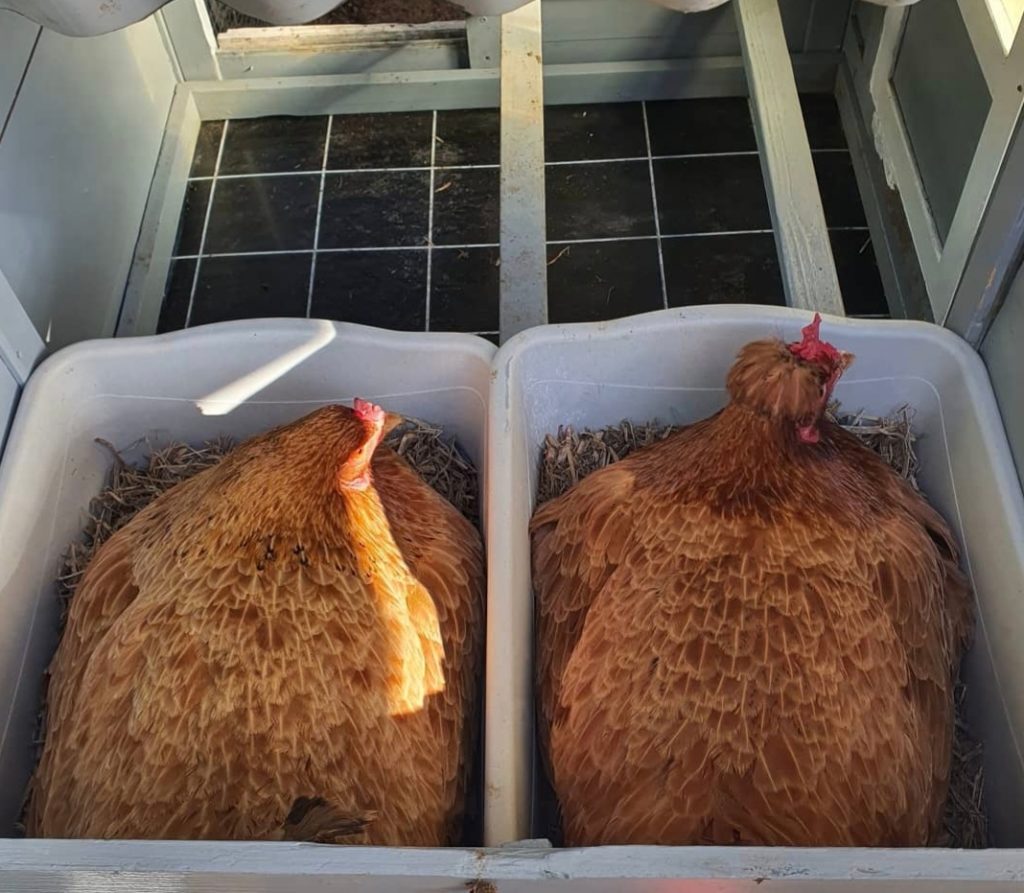
The quality of the incubator used and the proficiency of the broody hen during incubation are variables that we cannot control or fully ascertain.
The market offers a plethora of incubator brands, ranging from basic models constructed with minimal materials at an affordable price point to higher-end options manufactured by well-known brands. Each incubator operates differently, and merely setting it to 37.6 degrees does not guarantee that it will maintain that temperature accurately throughout the incubation process. While a friend or previous owner may have successfully hatched eggs using the same setting, it does not guarantee the same outcome for a new owner.
In an instance where two batches of eggs sourced from different breeders are incubated together, with Lot A placed on the right side of the incubator and Lot B on the left, it’s important to note that the disparity in viability between the two lots does not necessarily indicate that Lot B contained inferior eggs. Incubators often have areas with varying heat distribution, resulting in hot and cold spots. Lot B may have been situated in a colder area of the incubator that did not provide sufficient warmth for embryo development, thus affecting its viability. This issue is commonly observed among hobbyist-grade home incubators, particularly those available on platforms like eBay and Chinese imports.
Similarly, while broody hens are often regarded as excellent natural incubators, this is not always the case. Some hens may have lower body temperatures or may not possess the same level of incubation skills as others.
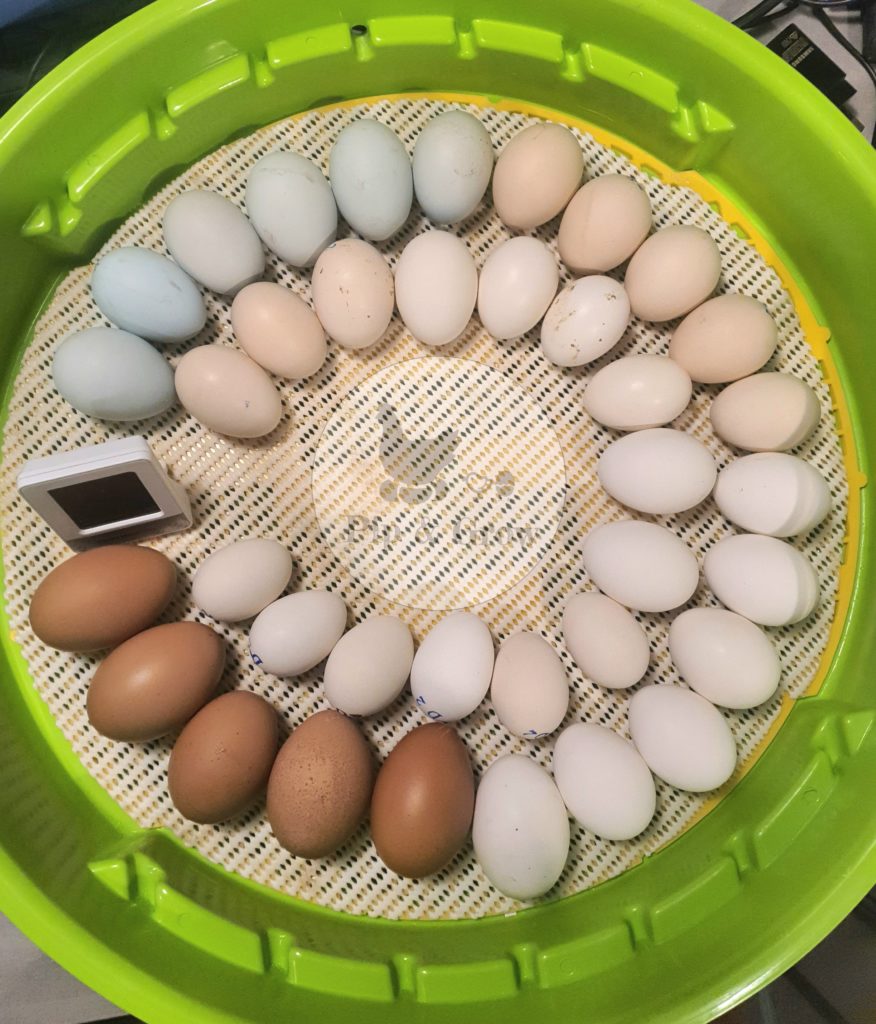
Customers vary greatly in their level of skill and knowledge when it comes to hatching eggs and these differences are beyond our control. Some may be seasoned hatchers with extensive experience, while others may be complete novices who have recently acquired their first incubator and are unfamiliar with the process. While some customers may have conducted research and have a basic understanding of concepts such as when to remove the turning tray or initiate lockdown, others may lack even this fundamental knowledge. There are fortunate individuals who achieve a successful hatch right from the start, but this outcome is often attributed to pure luck.
Reflecting on our own journey, we recall our initial experience of hatching 3 chicks from 24 fertile eggs using a cheap incubator at home. Since then, we’ve progressed to hatching over a thousand chicks every season. Along the way, we’ve gathered invaluable lessons from importance of quality incubators to adjusting incubation conditions. While there are established standards for egg incubation, adjustments are often necessary based on variables such as ambient humidity and temperature, which can vary widely depending on factors like the location of the incubator and prevailing weather conditions. Adaptation and learning are constant processes in the realm of egg hatching.
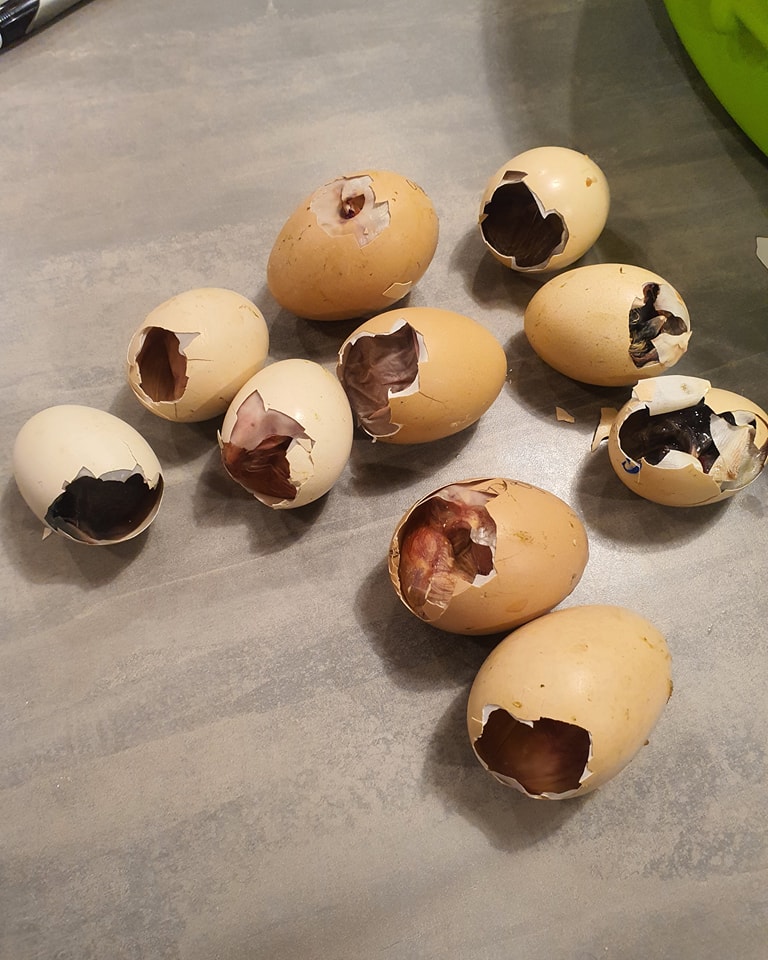
Various unforeseen events can occur during incubation, impacting the outcome. Power outages, whether noticed or not, can disrupt the incubation environment. Forgetting to add water to maintain humidity levels, experiencing a heatwave that overheats the eggs, or encountering malfunctions in the incubator are all potential scenarios.
We’ve encountered situations where despite setting the incubator for fully developed embryos in lockdown on day 19, none of the chicks successfully hatched. Investigation revealed that the temperature inside the incubator had soared to 42 degrees Celsius, far exceeding the intended 37.5-degree setting. Tragically, chicks have perished due to overheating even when the incubator appeared to be functioning correctly.
Similar challenges can affect broody hens during incubation. Wild weather may alter their behavior, rodents may disturb the nest nightly, other hens may attempt to lay on the nest resulting pushing the broody hen out, or mites may infest the nest, all of which can disrupt incubation and ultimately affect the hatch outcome. These unpredictable factors highlight the complexities and uncertainties inherent in the hatching process, whether using an incubator or relying on a broody hen.
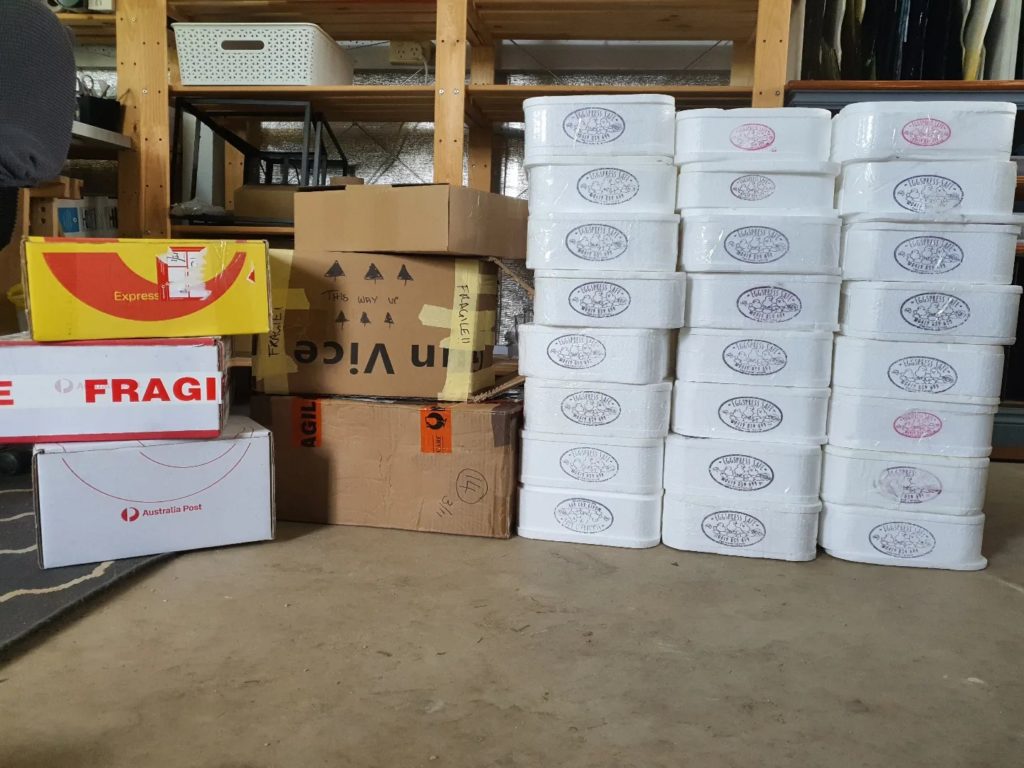
Contacting The Breeder
With experience both as breeders and consumers, we’ve gained insights into the challenges faced in the industry. Having purchased over 200 dozens of fertile eggs from breeders across Australia, we understand firsthand the disappointment that arises when things don’t go as planned, as well as how the tone of breeder communication can shift when issues arise.
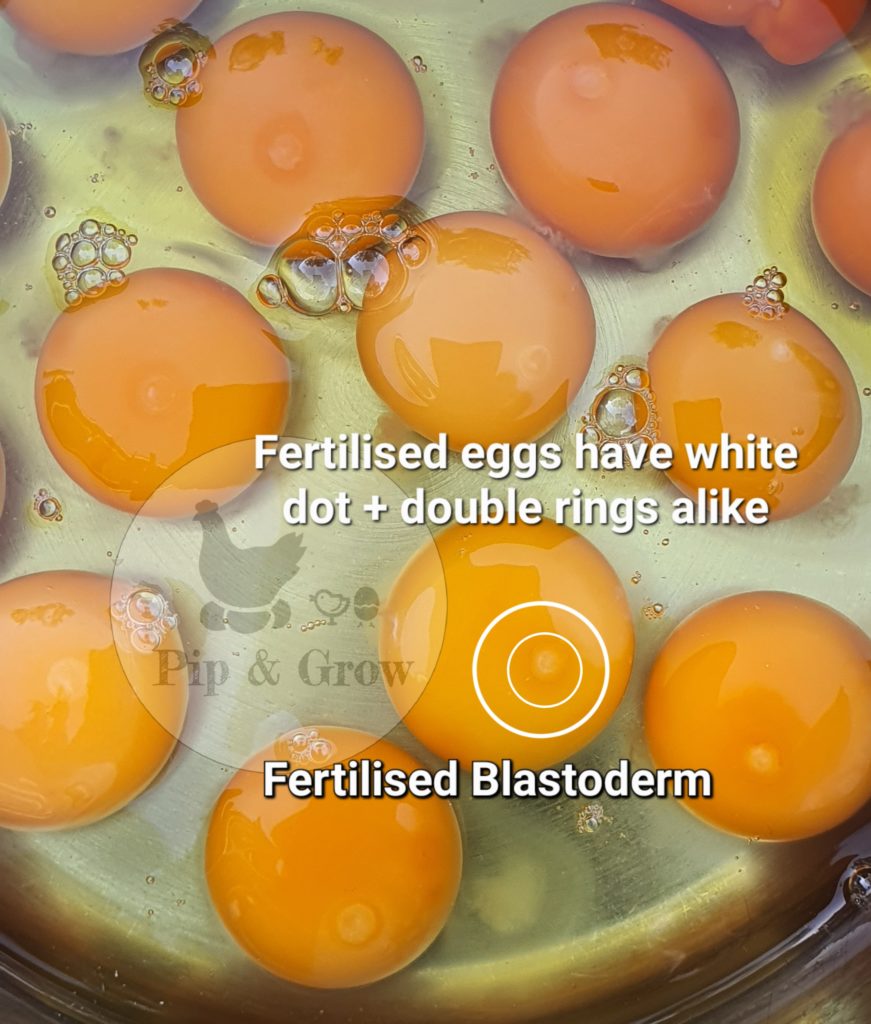
If you’ve purchased fertile eggs from a breeder and suspect there may be an issue with fertility, supported by appropriate evidence, we advise contacting the breeder immediately, ideally before day 7-10 of incubation, soon after the first candling. This demonstrates that you’ve followed recommended procedures and are proactive in addressing any concerns. It’s crucial not to discard the eggs until you’ve contacted the breeder, and be prepared to provide photos and videos if requested. The breeder may request to see a video of candling individual eggs to assess any damage to the air cell, or they may ask to crack open eggs to inspect the “Blastoderm,” which indicates fertilization. This underscores the importance of contacting the breeder at an early stage, as Blastoderm can deteriorate and become difficult to observe as eggs age inside the incubator.
Ultimately, from this point onward, it’s at the breeder’s discretion how they choose to handle the matter.
On another note, We strongly discourage contacting the breeder after hatching with a poor outcome, as there are numerous variables during the 21-day incubation period over which the breeder has zero control. These factors could have been addressed if the breeder was informed earlier. Prompt communication allows for potential issues to be addressed in a timely manner, increasing the likelihood of receiving assistance from the breeder.
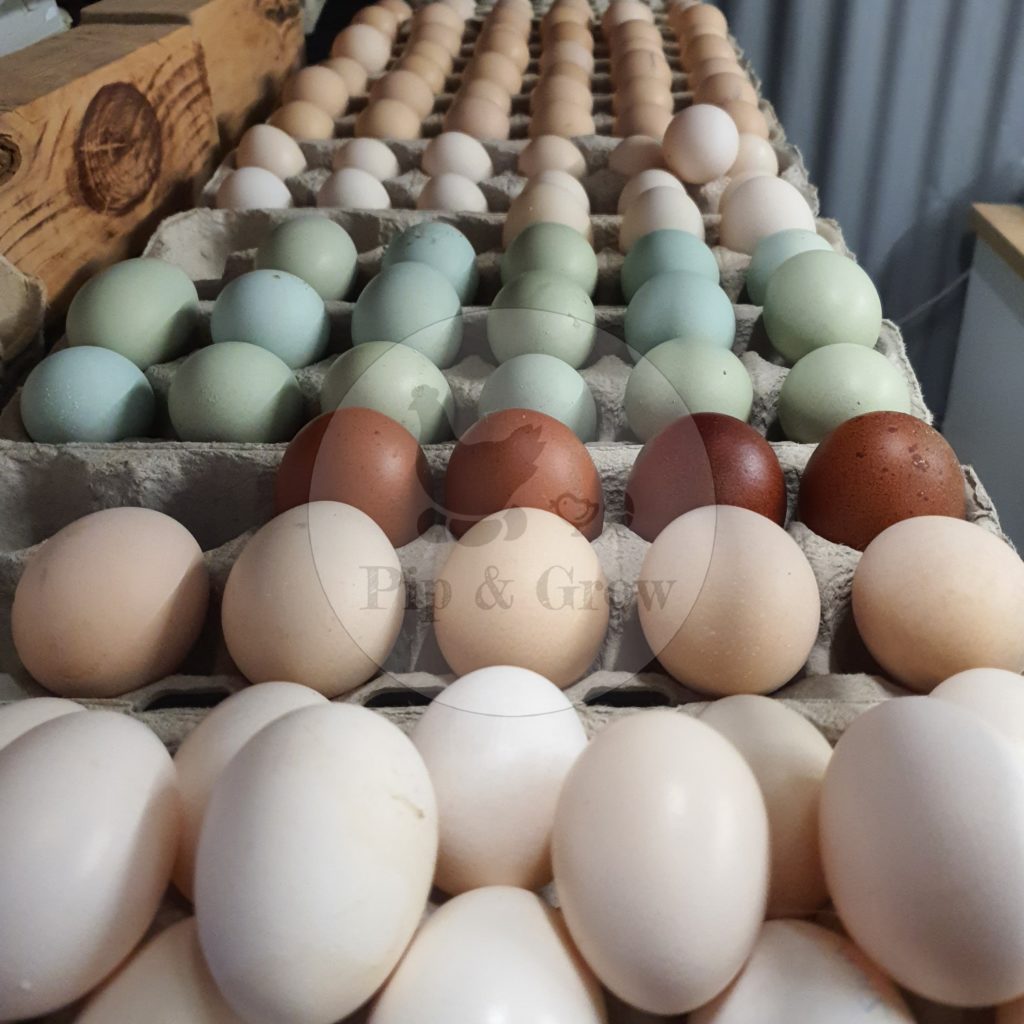
We firmly believe that a responsible breeder should prioritize listening to their customers and offering guidance whenever genuine inquiries arise. Furthermore, they should be ready to take responsibility if clear evidence suggests that there may have been an issue with the eggs they provided. This commitment to accountability and customer satisfaction is paramount in our approach to offering fertile eggs, and we stand firmly by this assertion.